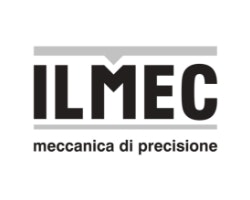
Production management in lathes and grinding
http://www.ilmec.it/2013/Needs
Digitising IT processes
Implement a highly specialized software product
Improving data transfer
Have a simple and intuitive interface to optimize the user experience
Implementation
There were three distinct phases: the project started with the centralized transfer of Colwin’s part-programs; this allowed to record and archive the machine’s ISO files without any further errors.
In a second step, the product was analyzed in all its phases, that is the traceability of lots and materials. Finally, in the last phase, the quality system and real-time production monitoring were implemented by networking the NC machines.
With the MES of MECMATICA, the company can now manage all processes at a computer level.
Results
Improvement of processes
Use of MECMATICA’s Spartacus Wireless with consequent reduction of cables in the workshop
More cleaning and order optimization from plants
Future developments and further implementations in 4.0 perspective
Interview with Paolo Cardinali - Owner
What is your core business?
ILMEC Srl - explains Mr. Paolo Cardinali - produces turned and rectified minute parts according to the customer’s design. We are specialized in the manufacture of shafts for motors and micro-motors. We also manufacture small items in various materials, especially stainless steel. Thanks to our technical expertise, ILMEC Srl can be appreciated and get in touch with many leading companies in the automotive, hydraulic and automation sectors.
How do you manage the quality system in your company?
I personally follow the internal quality system, derived from my previous work experience as an employee, is a system that I have expanded and made in our company one of the factors that makes us appreciate more in the subcontracting market, are very demanding when it comes to quality.
We work in the automotive industry, in the oil industry and recently also for the automation sector producing sensors of various types, are sectors where the demands for finishing the parts are similar to those of a high-end jewel, and despite the difficulties associated with hard-to-work materials, we are able to guarantee the technical specifications required by the customer that are always higher in all small or large production batches. To guarantee this we have invested a lot in the training of staff and in the realization of a very efficient metrological room equipped with the most modern instruments on the market.
Metronomo.Net has long been your production manager: what was the first impression?
I liked it very much from the beginning, I would call it a flash of lightning, I came from a previous of a competing software in DOS and with less graphics. As soon as I saw Metronomo.Net the system I liked, in 2010 came to us the Sales Director of MecMatica, Mr. Arnaldo Bollani, and we began to know each other.I remember that first of all I was impressed by the data transfer, it has a simple interface, intuitive and easy to use for the operator in the office. In the early years of the Metronomo.Net system, in collaboration with MecMatica, we were the first to bring the drawings and measurements acquisition on the operator’s console, also we were the first workshop in the area of Ancona to digitize processes with information technology.
Why did you choose the MecMatica software?
I gave them confidence because MecMatica has behind years of experience in the mechanical sector and I wanted a highly specialized software product, it is undeniable that their Metronomo.Net system is what the market offers the best management of production in our sector. Already in 2011 MecMatica was far ahead of their national competitors, both from a technological point of view and as experience gained in the field in precision workshops.
Why choose a MES system?
Metronomo.Net is a valuable tool and important support in the ISO 9001 certification and management, in all sincerity with the Metronomo.Net Mes our company can manage everything electronically.
How was the project managed?
The collaboration with MecMatica was very important for the success of the project. In particular MecMatica can count on a team of zealous and close-knit technicians.
The technicians are available to meet our specific needs, often dictated by our way of working. These years were also characterized by mutual esteem with the technical director of MecMatica, Mr. Cavalleri Diego, with whom we have made important and significant collaborations over time.
What were the stages of implementation?
There were 3 distinct phases, we started with the centralized transfer of the Colwin part-program, this allowed me to record and store without any more errors the ISO files of the machine. In a second step, we set ourselves the goal of identifying the product at all its stages, that is, the traceability of batches and materials. In the last phase we have implemented all the quality system and real-time production monitoring by networking our NC machines.
Why did you opt for a Wi-Fi solution?
For the transfer of programs between the different solutions proposed, I chose the Spartacus Wireless by MecMatica because at the time I did not want too many cables in the workshop, taking care of cleaning and order from the plants, MecMatica’s Spartacus Wireless solution addressed the monitoring needs of NC machines and integrated well with our production infrastructure. In 2010 they were the first to offer this technology in workshops, developed by MecMatica with a box all in one Wi-fi on board CN machine. For the future we are planning further developments and implementations also in 4.0 perspective.
What are the management developments with Metronomo.Net?
Production scheduling is a module of Metronomo.Net that we would like to start using more effectively, along with the advanced statistical analysis part of Prograph’s production, which may have really interesting implications because it is an impartial eye on the performance of machines in production.