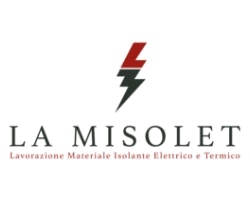
Electrical and thermal insulation material processing
https://www.misolet.it/Needs
Need for increased production capacity
Management of a large number of contracts
Move in an industrial and structured direction
Replace management with Excel sheets
Implementation
After evaluating three different management proposals, the final choice fell on MecMatica, which was later found to be already supplying a well-known company. Currently, eight people in the office use Metronomo.Net daily on different levels, plus operators who deal with declarations of work stages in production.
The activities were not limited to configuration and training on the Metronomo.Net software, but involved a consultancy phase to optimise the management of business processes in the various departments, including the office.
Results
Ease and speed in finding the necessary information gathered in a single integrated management environment on the various business functions
Real-time control of production and order progress
Management of production up to DDT loading and unloading
Interview with Giovanna Addabbo - Owner
What kind of company is La Misolet Srl?
We are a company that operates in the subcontracting market for over 50 years. Today we have a staff of 30 employees with a modern fleet of CNC machines, also palletized, for machining both plate and round.
Our operations also include the cutting and assembly of insulating articles, including metal parts.
In what field do you work?
Our sector is the processing of electrical and thermal insulation materials, such as bulletin boards, glazing, heat insulators, plastics, etc. Our products are intended for a mix of industrial applications: low, medium and high voltage electrical sector, electromechanical, energy and renewable sources, automotive, space and defense, nuclear and railway. We are subcontractors with a high degree of specialization of the major international realities.
What are your production batches and skills required?
For the mechanical processing we range from samples to small batches, up to thousands of pieces, reaching millions as far as cutting is concerned.
Our sector is very diverse in terms of demand and the skills required are very specific. We are one of the few structured companies on the market able to work the most diverse types of materials listed above. The constant supervision of our technical office has led us to offer a real consulting service in response to specific requests for thermal insulation, electrical, mechanical resistance etc. , often contrasting with each other, so that they have to be harmonized by studying the physical and mechanical properties of materials.
Have you tackled new subcontracting areas?
Wherever an insulating material is required, we seek a solution for the customer, recently we have also entered the packaging sector by providing details for the construction of packaging and packaging machines.
What are your strengths?
One of our strengths is our expertise in processing and sourcing specific quality materials to ensure that the material itself, produced largely by stratification, does not contain impurities such as to cause serious problems on the final workpiece being processed.
The quality flow of La Misolet starts from the purchase of the raw material until the delivery of the finished product that we guarantee in different times depending on the complexity of the order and the batch required.
We also offer the service of cut to size, the service of calibration and the direct sale of the various materials in plate.
Our added value is also the consulting service offered by our technical office to customers. We are also a dynamic company, a fundamental characteristic in an increasingly demanding market, and where the technological evolution requires thorough and constant updates, professional expertise and the use of materials more and more safe and reliable.
This mix of skills enables us to obtain a value for money that is certainly interesting.
What was the need to choose a new manager?
At first, we have faced the growth of customer orders by moving from Milan to Codogno in order to have a greater production capacity by increasing space and machinery. We soon realized that even the management software had to evolve towards an industrial and structured direction, the classic Excel sheet used in the past to manage orders was now obsolete.
What kind of software selection did you do?
We noticed MecMatica Srl thanks to its numerous communication tools: web, mailing, advertising in print magazines, and later we met at the fair. After evaluating 3 different management proposals, our final choice fell on MecMatica and later discovered that they were already suppliers of a plastic material processing company with which we have been working for years: Robecchi Articoli Tecnici.
Today who uses the Metronome Software in the Company?
Currently 8 people in the office use Metronomo.Net daily on different levels, to which are added operators who deal with declarations of work stages in production.
How were the technical activities carried out?
We have found in Mecmatica a consultant with specific experience in production, the activities were therefore not limited to configuration and training on the Metronomo.Net software, but they involved a consultancy phase to optimise the management of business processes in the various departments, including the office.
We are satisfied with the training. The introduction of the new management system was not easy, and we also had to adapt to a different management of weights and material forms.
Today, 2 years after the first order we are finally operational and satisfied with the investment made on the Metronomo.Net management system.
Metronomo.Net has been operating in the company for several years, what benefits have been brought?
Certainly it is easier and faster to find the necessary information, we find them in a single management environment integrated on the various business functions. The production situation and the progress of orders is always under control in real time, compared to when you had to go to the production departments to retrieve data.
Thanks to Metronomo.Net we manage the production up to the DDT of loading and unloading, while the invoicing part takes place with our historical administrative. I must admit that the speed and flexibility of Metronomo.Net have pleasantly surprised me and it has proven to be a complete and modular software.
So you consider yourself a 4.0 supplier thanks to the new management system?
Yes, the credit is due to MecMatica’s sales representative, Mr. Federico Catteruccia, who at a meeting explained the advantages of the Calenda plan in 2018. We were in fact buying 2 new CNC machines, but we had not fully grasped the meaning of 4.0 and the tax advantages resulting from the union with the production management. We then proceeded to monitor and connect all our CNC machines, including 12 machining centres. Today after 2 years I would say that we are a 4.0 supplier in fact.
Strategies and plans for the future of La Misolet?
In Codogno we were at the center of the Covid-19 storm first in all of Italy, but fortunately our production was only stopped 2 weeks obviously with all the organizational problems you can imagine. The first red zone in Italy suffered mainly from a lack of reliable information on what to do and how to deal with the situation. We have never been short of work and our Ateco code has allowed us to operate even in full emergency with all the necessary health precautions, although in limited shifts and ranks of staff.
For our future we are building a new production site right here in Lodi, which will be operational from next year in order to double the working spaces.
We work in a very specific machining market with horizontal integration of applications, so if one sector often slows down another sector fills the demand gap. Our company has been active for over 50 years, this means a solid reputation among customers from various sectors. This is our strength, a desire to do that we hope will be shared in Italy and the world at a difficult time like the one we are living.