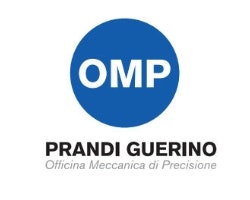
Design, analysis and manufacture of precision mechanical components
http://www.omprandi.it/Needs
Need to replace a system that did not support business change
Have a larger graphical interface
Modernization of software
Search for a complete and modular suite
Implementation
The collaboration started at the end of 2015 and was the ideal solution for a scalable and step by step integration, despite some initial fears in the transition data from old to new system. Three operational phases have been developed with synergy between them: in-depth preliminary technical analysis; constant management consulting to map and optimize the procedures and our business flows; training on the various modules of Metronomo.Net purchased.
Today the software is used by all the operators in the workshop for the declarations of advances commissioned in production with seven touch screen stations installed in the two main departments. In addition, it is used by the owner Giovanna Prandi and the Quality Manager.
Results
Improved user interface
Smooth access to information
Ease of extraction of economic and production reports
Export of data to tables for in-depth information management
Sharing information with all staff
Interview with Giovanna Prandi - Owner
"We have been a family-run company for generations, today we have a staff of 30 motivated and professional employees who have always been involved in the main business choices."
How has your work evolved over the years and what is your core business?
Certainly over the years we have witnessed a constant growth of the company towards specialization and precision in processing. The demand for increasingly complex projects from customers has led us to outline a strategy that involves continuous investments in technology and constant professional growth of our operators.
Our core business consists in the supply of mechanical parts for the sector of CN machine tools, our customers are in fact important Italian and foreign manufacturers with whom we have been working for over 40 years. We supply them with various types of parts such as grooved shafts, ISO and HSK spindles, rods and special accessories and we follow them in the various stages of the realization of their details.
Have you dealt with other sectors in precision subcontracting?
Always remaining in the machinery sector, we have provided important details for marble processing, for the textile machinery sector, for food packaging and also for aeronautics.
We produce both single pieces and medium-sized batches with an adequate and diversified machine park; the internal working stages of the company are: turning, deep drilling, milling, dentating, adjustment, grinding, balancing and we also take care of some internal heat treatment steps.
Our services are also managed and supervised by a strict quality control system.
What are the strengths of OMP Prandi?
Certainly our operational flexibility: we are able to adapt quickly to the customer’s requests even during construction. In addition, we can always rely on the knowledge and skills of our highly qualified operators, guaranteeing the highest quality of our parts and customer satisfaction.
Our company invests a lot on young people, once they are inserted in the team are followed by expert tutors through training "on the job" and through corporate courses on various current issues.
What was your motivation for choosing a new management software?
At the end of 2015 we realized that our old AS400-based system was no longer able to withstand the business changes required: Its limited graphical interface and the impossibility of updating it to something more modern were the main reasons for the change.
What kind of Software Selection did you do?
We mainly rely on web research and have called a number of possible suppliers, including MecMatica Srl. In addition to the change of the Administrative Software part we were looking for a complete and modular suite for production management in its various aspects. Metronomo.Net immediately seemed complete and scalable step by step, although some initial fears in the transition from the old to the new system slowed down our decisions. In addition, the integration with the new administrative system had to be managed and customizations were needed in the data flow between the 2 systems.
Today who uses Metronomo.Net in the company?
Today the software is used by all the operators in the workshop for the declarations of the advances commissioned in production with as many as 7 Touch screen stations installed in the 2 main departments. In addition, I use it personally and also the Quality Manager.
What advantages have you found with Metronomo.Net?
Certainly the user interface allows us to access information with more fluidity than in the past and it is easy to extract from Metronomo.Net the economic and production reports. Personally, I found myself very well also exporting the data in tables useful for a thorough management of the information. The software has also become a common information sharing system that allows us to analyze together with our Production Manager and the personnel involved the progress of production.
How was the technical activity managed?
An excellent relationship has been established with MecMatica’s management analyst Ing. Davide Taborelli, who has been with us since the first day of this project and has always been available to our requests. We had 3 operational phases which were mutually reinforcing: we started with a preliminary in-depth technical analysis, which was followed by a real and constant management consulting in order to schematize and optimize the procedures and our business flows and finally training on the various Metronomo.Net modules purchased. All this also managing our various requests for changes that emerged and were agreed during the management analysis. It has been challenging work for all of us, which is producing the expected results.
To what extent could Metronomo.Net make OMP a Company 4.0?
The recent Covid-19 events have forced OMP Prandi, like other Italian companies, to review operational priorities and only reserve for the moment the connection of machine tools in real time. We know that with MecMatica we are in good hands from this point of view and we hope to take up the topic CN 4.0 as soon as possible, probably with a Wireless solution.
What strategies do you have to manage the ongoing change?
Our expansion plans included the possibility of expanding the production site and offices, together with a diversification of services and work offered. Unfortunately, the recent events and restrictions imposed for just health reasons, force us to postpone our expansion plans. We are waiting for a resumption of orders, confident that we will be able to seize the opportunities presented thanks to the expertise that OMP Prandi has been able to mature and consolidate over time in more than 70 years of activity.